Chamfering
When Precision Matters
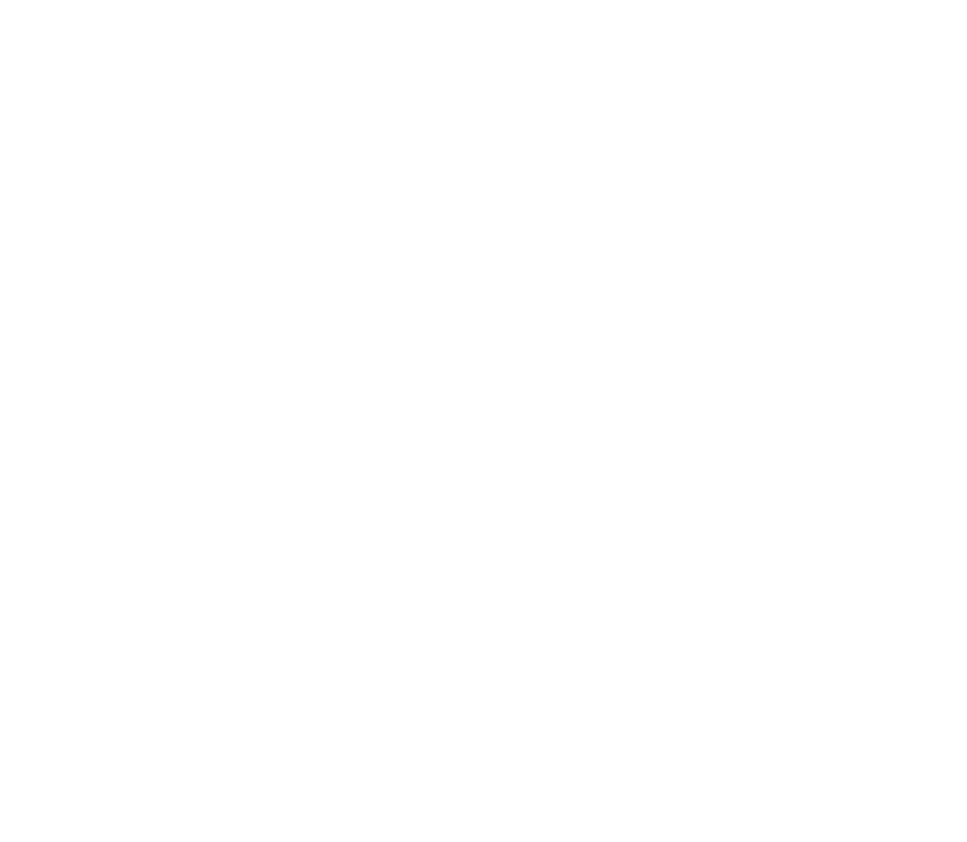
Erix Chamfering Tools: Precision engineering for efficient machining
Chamfering is the process of beveling or rounding the edges of a workpiece or hole. This operation serves not only to enhance the aesthetics of the workpiece but also to eliminate sharp edges, which can pose safety concerns.
Erix Tool AB has been making precision chamfering tools for 40 years, with a proven track record of excellent performance on a wide range of materials.
Compact and efficient, the Erix chamfering tool is the ideal solution for chamfering in confined spaces, such as those found on engines, turbines, and pumps. These innovative tools consist of a spindle and a cutter, known as a wing. The unique patented design ensures reliable performance with only one moving part.
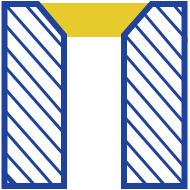
Chamfering tip:
To improve the finish on the chamfered surface, lower the speed and feed at the end of the operation and let the tool rest for a few seconds.
What is Our Chamfering Tool Used For?
Erix tools excel at back spotfacing and back chamfering, making them indispensable in various machining applications. They are the go-to choice for tasks involving spotfacing, chamfering, counterboring, and deburring.
Materials The Tool Can Drill Into
These versatile tools can handle a wide range of materials, making them suitable for diverse machining needs. Whether you’re working with magnetic soft steel, structural steel, alloy steel, or even thermoplastics and synthetic materials, Erix chamfering tools deliver exceptional results.
Technical Specifications of Our Chamfering Tool
Erix chamfering tools are engineered to precise standards to deliver the best results. The spindle’s pilot part guides the tool into the hole and takes up cutting forces, ensuring efficiency. The pilot diameter is carefully calibrated to the nominal hole diameter, offering superior performance. The wings are designed with high-speed steel (HSS) for smaller sizes and feature square or rectangular inserts for larger wings. These inserts are securely clamped using Secodex left-hand threaded screws.
In addition to vast savings in terms of efficiency and productivity, as well as the obvious environmental benefits, automating the chamfering process ensures 100% consistency between the critical dimensions and significantly reduces the risk of mechanical failure or human error.
For perfect chamfering results, make sure to consult our basic guide.
Common chamfering techniques
Chamfering is often performed at angles of 45°, 60°, or 30°, depending on the material and application. Erix Tools also offers custom angles tailored to specific needs, allowing for greater flexibility in various machining tasks.
Typical problems and solutions
Common chamfering issues include vibrations and poor surface finish. To solve these, adjusting feed rates and using proper coolant is essential, which helps prevent tool overheating and ensures better surface quality.
Chamfering applications across industries
Chamfering is widely used in industries like manufacturing, automotive, and aerospace to smooth edges, improve part fitting, and prepare surfaces for welding or assembly.
Find out where you can buy our tools here.
Technical information
In addition to our standard chamfering tools (shown left), we also supply semi-standard tools as well as custom spindles, wings and shanks. Refer to the diagram of the Erix Tool in our catalogue for part details.
For example:
- Non-standard chamfering angles, minimum 15°
- For holes up to ø 200 mm
- For holes with ø intervals of 0.05 mm (ø 4.5 – 9 mm)
All spindles from ø10 upwards (hole size) with cylindrical shanks are designed for Weldon fastening (DIN 1835B).
All spindles from ø10 upwards (hole size) are available with a Morse Taper (27-25-MK3) rather than a a cylindrical shank.
Please refer to our catalogues* for full information about capacities, dimensions, combinations, materials and standard part details.
* Available in both metric (mm) and imperial (inches) measurements.
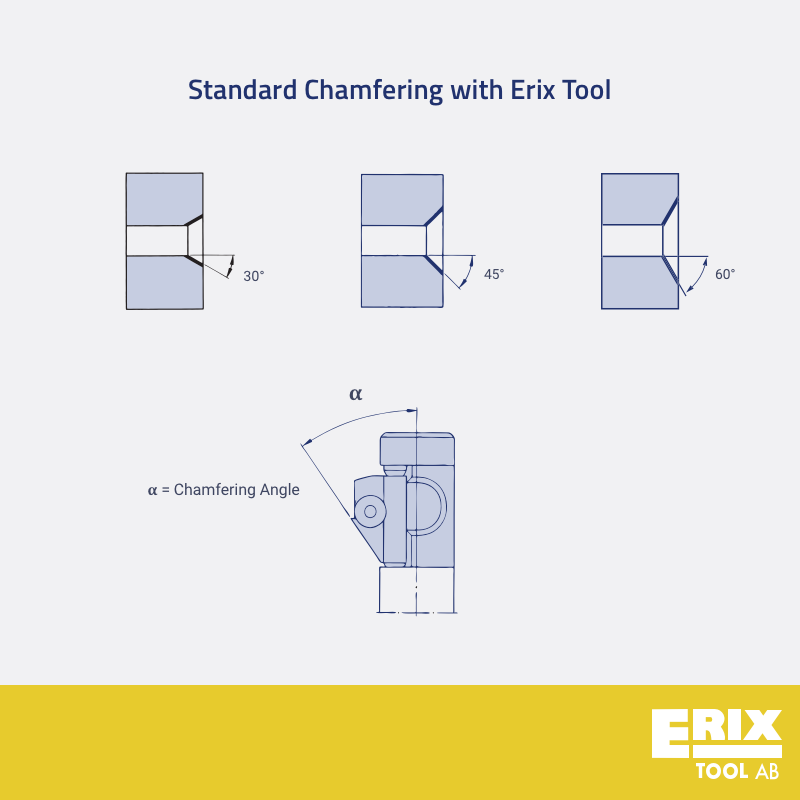
What is the purpose of chamfering?
The main purpose of chamfering is to eliminate sharp edges, making components safer to handle and improving their aesthetic appeal. Chamfering is commonly used in areas such as automotive parts (e.g., bolts and fasteners), metal piping, machinery components, and for preparing holes for screws and nuts to ensure proper fit and facilitate assembly or welding processes.
What is the difference between chamfering and bevelling?
Chamfering creates a 45° angled edge to remove sharp edges. Bevelling cuts a deeper edge at a specific angle, often for welding preparation.
What is an example of chamfering?
An example of chamfering is smoothing the edges of a kitchen countertop or furniture piece to prevent injury and make it more comfortable to use. In an industrial context, chamfering is also used on metal pipes to ensure safe handling and a proper fit during assembly.
What is the process of chamfering?
The chamfering process involves selecting a suitable tool, setting the spindle speed and feed rate, and ensuring proper alignment of the workpiece. The tool then bevels the edges at an angle, typically 45°, while coolant is used to maintain temperature and prevent overheating.
What is a chamfering tool?
A chamfering tool is a cutting instrument designed to create a beveled or rounded edge on a workpiece or hole. This process not only enhances the aesthetics of the workpiece but also eliminates sharp edges, which can pose safety concerns. Chamfering tools are essential in various machining applications, including spotfacing, chamfering, counterboring, and deburring.
What is the difference between tapering and chamfering?
The distinction between tapering and chamfering lies in how the material’s dimensions are altered. Tapering involves a gradual reduction in a specific dimension along the length of an object, resulting in a conical shape. In contrast, chamfering entails cutting off the edge between two surfaces at a specific angle, creating a beveled edge without significantly changing the object’s overall form.
Download a Catalogue
Four good reasons
Robust & durable
The Erix cutting tool’s solid dependability is ideal for situations where downtime is unacceptable.
Simple & user friendly
A simple, rapid cutting wing replacement system makes the Erix cutting tool extremely efficient and user-friendly.
Versitile & convenient
With cutting wing sizes ranging from 8 mm to 15.6 cm few cutting tools are as versatile as the Erix Tool.
Manual & automated
Find a distributor
The Erix Tool is available through a large network of authorised
distributors and agents around the world